재고관리
재고
- 현시점 이후에 사용할 목적으로 기업이 보유하고 있는 원자재, 부품, 완제품
- 재고가 부족할 경우 : 고객 수요 충족 x -> 손실 발생
- 재고 너무 많은 경우 : 원가에 부담
적정 수준의 재고를 확보하여 관리하는 것이 기업의 경쟁우위에 중요한 요소
재고와 관련된 비용
> 재고를 줄여야 하는 이유
재고 유지를 위한 비용 발생
재고유지비(holding cost) : 품목을 보유하는데 들어가는 비용
이자, 보관비, 취급비용, 세금, 상품훼손, 보험비 ...
일반적으로 재고 1단위를 1년간 유지하는데 들어가는 비용은 그 가치의 20~40% 이름
● 기회비용
다른 투자 기회 상실로 발생하는 비용
● 보관/임대 비용
창고 공간 임대 비용, 다른 용도로 사용할 수 있는 기회 비용
● 세금 및 보험료
재고량 증가 - 부과되는 세금, 보험료 증가
● 진부화 및 훼손
제품의 진부화 : 재고 보관기간이 길어짐으로 인해 제품의 가치가 떨어지거나 아예 못쓰게 됨
> 재고를 비축해야 하는 이유
재고유지비용을 줄이기 위해서 재고는 적을수록 좋다
그러나 다음의 이유로 인해 일정 수준의 재고를 보유하는 것이 오히려 유리할 수도 있다.
● 고객응대
재고 고갈(stock out) : 재고가 없어 물건을 팔지 못 하는 경우
미납 주문(back order) : 고객의 주문을 약속시간에 충족시키지 못해 고객에 대한 신뢰를 떨어뜨리거나,
할인을 해줘야 하는 일이 발생함
● 주문 비용
주문 비용(order cost) : 주문할 때마다 발생하는 비용
준비 비용(setup cost) : 생산 품목을 교체할 때 설비 가동을 위한 비용
품목 교체를 자주하면 재고를 줄일 수 있지만 그만큼 준비비용이 증가
● 수송비용 및 구매가격
재고가 많은 경우 차량 적재율을 높일 수 있어 수송 비용 감소
일시에 많은 양을 주문함으로써 구매 단가가 낮아짐(재고비 < 가격할인)
재고 유형
> 주기 재고
총재고 중에서 로트(lot) 크기에 따라 직접적으로 변하는 부분
○ 로트 : 한 번에 주문하는 수량
=> 로트 크기는 주문 간격에 비례함
주문과 주문 사이의 간격(주문 간격)이 길수록 주기재고 양 증가
주문 간격이 짧을수록 주기재고 양 감소
○ 1회 주문량 : Q 평균재고 = Q/2
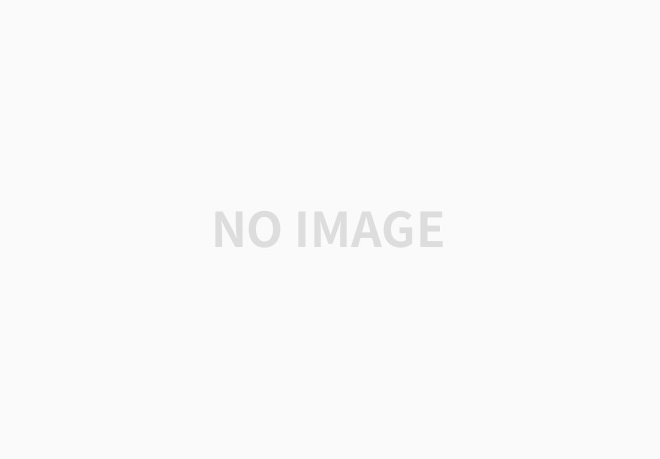
> 안전 재고
고객 서비스의 차질과 재고 부족으로 인한 기회 비용의 발생을 예방하기 위하여 비축하는 재고
제품 수요, 리트 타임, 공급업체의 불확실성에 대처하기 위한 재고
○ 리드타임 : 주문에서 납품까지 걸리는 시간
○ 안전재고 비축 방법 1. 예상되는 수요보다 많이 발주
2. 평균 리드 타임보다 일찍 발주

> 수송 재고
한 지접에서 다른 지점으로 이동 중인 재고
납품업체 -> 유통센터, 유통센터 -> 도매점, 도매점 -> 소매점으로 이동중인 재고
이미 발주를 했으나 아직 도착하지 않은 재고
재고 모형
재고와 관련된 문제를 해결하기 위하여 주어진 상황에 몇 가지 가정을 추가하여
재고와 관련된 비요을 최소화하는 문제를 해결할 수 있도록 해주는 모형
> 확정적 모형 : 수요와 리드 타임이 고정되어 있는 경우
● (고전적) EOQ 모형
● 재고 부족이 있는 EOQ 모형
● 가격 할인이 있는 EOQ 모형
> 확률적 모형 : 수요와 리드타임이 불확실한 경우
● 정량발주 모형
● 정기발주 모형
● (s, S) 시스템
확정적 재고 모형
수요와 리드 타임이 고정되어 있는 경우
> (고전적) EOQ 모형
주문(발주)비용, 재고유지비용만 고려
- 경제적 주문량(EOQ) : 재고와 관련된 제 비용을 최소화할 수 있는 가장 경제적인 1회 발주량
● EOQ 모형의 가정
발주비용은 매 주문마다 일정(발주량의 크기와는 무관)
재고유지비는 발주량의 크기와 정비례(=재고수량과 정비례)
품절 인정하지 않음(=재고부족 존재 X)
구입 단가는 발주량의 크기와 관계없이 일정
재고 사용 비율(수요율) 일정
조달에 걸리는 시간(리드타임) 일정
● EOQ 공식 유도
주어진 값들
S : 1회당 발주비(setup cost)
D : 연간 수요(Demand)
H : 단위당 재고유지비(Holding cost)
결정변수 : Q = 경제적 1회 발주량
연간 총비용 = 연간 발주비 + 연간 재고유지비
TC = Q*H / 2 + D*S / Q
= 루트√2DSH
연간 발주비 = 연간 발주횟수 X 1회당 발주비용
= (연간 수요 / 1회당 발주량) X 1회당 발주비용
= D/Q X S
= D*S / Q
연간 재고유지비 = 연간 평균재고량 X 단위당 재고유지비
= Q/2 X H
= Q*H / 2
연간 재고유지비 Q 정비례, 연간 발주비 Q 반비례
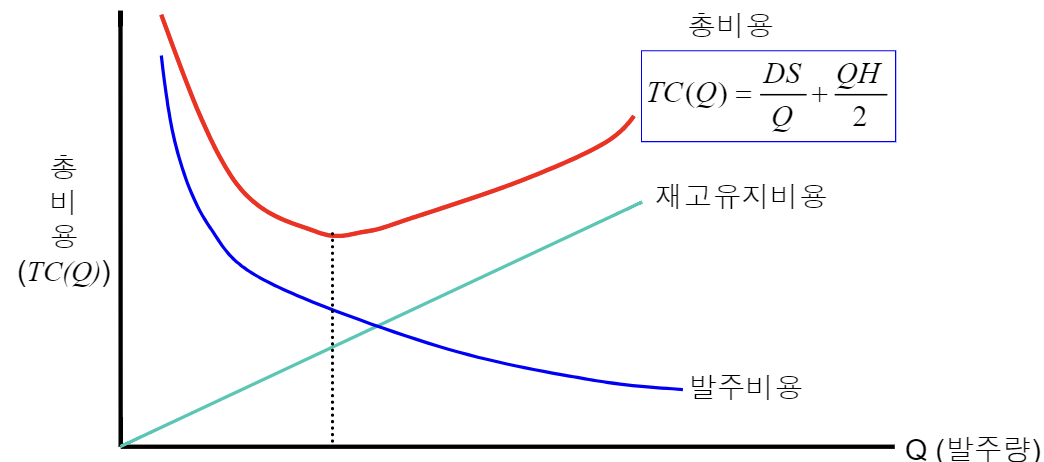
총비용이 최고가 되는 Q = 1회 경제적 주문량
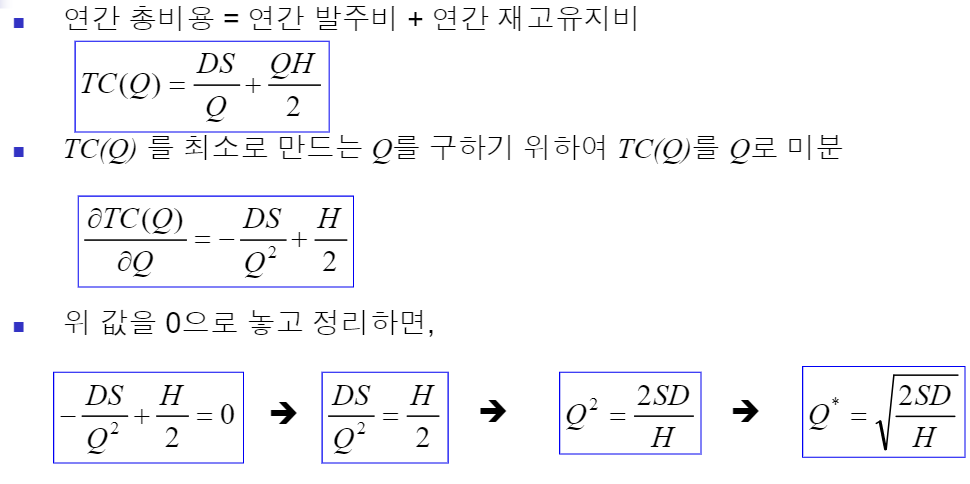
TC는 Q함수이므로 TC(Q)를 Q에 대해서 미분하고 0으로 놓고 Q에대해 정리
최적 발주 횟수 = 연간 총수요 / 경제적 발주량 (D/Q*)
최적 발주 간격 = 경제적 발주량 / 연간 총수요 (Q*/D)
(분모 클수록 값 작아짐, 분자 클수록 값 커짐)
> 재고 부족이 있는 EOQ 모형
고전적 EOQ 모형 + 재고 부족비용 고려 모형
연간 총비용 = 연간 발주비연간 + 재고유지비 + 연간 재고부족비
TC(r) = DS/Q + (Q-Y)^2H/2Q + Y^2R/2Q
연간 발주비 : DS / Q (고전적 EOQ 모형과 동일)
연간 재고유지비 = 한 주기당 재고유지비 X 연간 발주횟수
= (Q-Y)^2H/2D X D/Q
= (Q-Y)^2H/2Q
단위당 연간 재고부족비 : R
연간 재고부족비 = Y^2R/2Q
경제적 발주량 Q* = 루트√ 2SD/H X 루트√H+R/R
최대 부족량 Y* = Q* X H/H+R
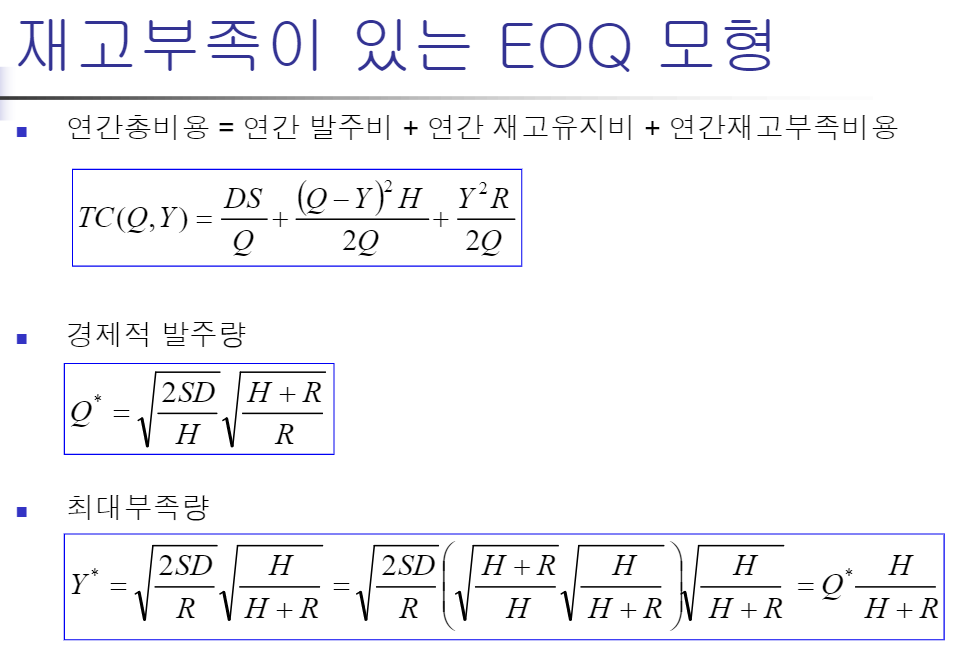
> 가격 할인이 있는 EOQ 모형
1회 구매량이 증가함으로써, 제품 가격을 할인 받을 수 있는 경우
(대량 구매에 따른 재고유지비용이 증가하지만, 이보다 가격 할인에 따른 이익이 더 클 때 적용)
할인되는 구간, 할인되지 않는 구간 EOQ 계산 후 구매가격의 합 계산하여 최종 EOQ 계산
총비용 = 발주비 + 재고유지비 + 구매 가격
TC = DS/Q + QH/2 + DP
EOQ (고전적 ) = 루트√2SD/H
확률적 재고 모형
확정적 재고 모형 : 재고가 사용되는 비율과 조달에 걸리는 리드 타임이 일정하다는 가정에 근거
그러나 실제 상황에서의 재교 변화는 매우 불확실
확률적 재고 모형 : 수요 변화가 확률적 분포를 가지는 것을 고려한 모델
=> 불확실성에 대비하기 위해 안전재고 보유
안전재고의 수준은 정책적으로 결정한 서비스 수준에 의해 정해짐
서비스 수준 : 고객으로부터 주문을 받았을 때, 품절을 일으키지 않고,
이미 보유하고 있는 재고에 의하여 물품을 공급하는 비율
ex) 서비스 수준 95% = 5% 품절위험수준 : 100번 중 95번은 주문 받은 즉시 공급
= 확률적 모형은 정책적으로 결정한 서비스 수준을 유지하기 위한 안전재고 수준을 결정하는 의사결정
● 정량발주 모형
재고량이 일정 수준(=재발주점)이 되면, 정해진 수량(=발주량, EOQ 추정치)만큼 발주
● 정기발주 모형
정해진 시점(=발주시점)에 정기적으로 미리 정해놓은 재고수준(=목표재고수준)이 되도록 발주
● (s, S) 시스템
정량발주모형 + 정기발주모형
> 정량발주 모형 (FOQ, Q시스템)
- 경제적 발주량, 재발주점의 결정
재고 수준이 일정수준(재발주점)에 도달하면, 사전에 정해진 수량(Q)만큼 발주하는 재고관리 방식
고정 : 입고되는 수량(Q) / 변동 : 리드타임, 발주간격, 최대재고수준
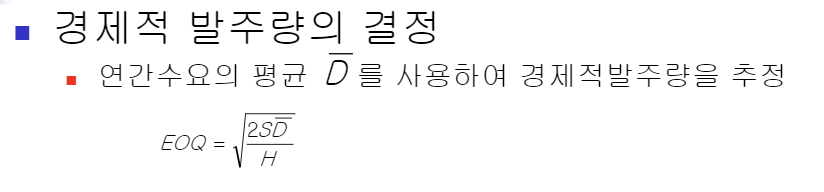
재발주점의 결정
- 재발주점은 서비스 수준에 따라 결정
- 재발주점 높으면 서비스 수준 높아짐(품절위험 낮아짐)
- 재발주점 낮으면 서비스 수준 낮아짐(품절위험 높아짐)
- 재발주점은 리드타임 동안의 수요와 안전재고의 합으로 결정
재발주점 = 리드 타임 동안의 평균 수요 + 안전재고
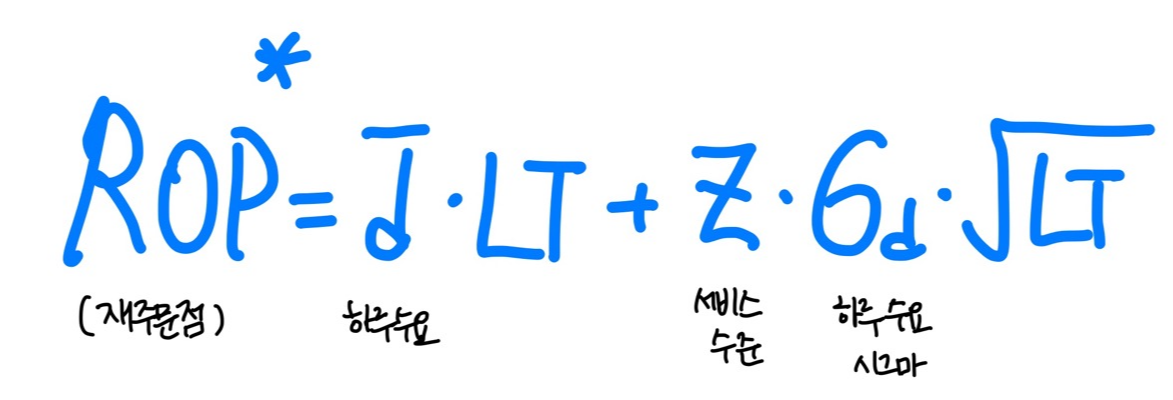
> 정기발주 모형 (FIO, P 시스템)
- 발주 간격(P), 목표재고수준(T)의 결정
재고수준을 정기적으로 조사하고 그떄마다 재고 수준을 일정한 목표수준까지 끌어올릴 수 있는 수량을 주문하는 시스템
재고 수준 연속적 조사 X - 정해진 기간이 경과한 후 주기적으로 조사
고정 : 주문 간격 / 변동 : 주문량, 발주 수량
발주시점에 도달하면 목표재고수준(T) - 현 재고수준 차이만큼 발주
발주 간격(P) = 경제적 1회 발주량 / 연평균 수요
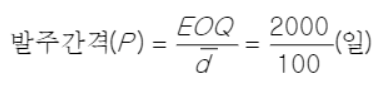
목표재고수준(T)

다음 주문시까지의 기간(P)와 주문에서 입고까지의 기간(LT) 동안의 수요 변화에 대응할 수 있는
안전재고를 확보하도록 주문해야 함 => P+LT 도안의 수요 불확실성 대비할 수 있는 목표수준 설정
> 정량발주(Q 시스템) VS 정기발주(P 시스템)
● Q시스템
여러 품목의 재고를 관리할 때, 품목별 조사 빈도를 다르게 설정 가능
로트 크기가 클 경우, 수량할인을 고려한 발주량 결정 가능
P 시스템에 비해 안전재고 수준이 상대적으로 낮음(매일 확인해서 재고수준 재발점 도달하니까)
● P 시스템
연속적 재고관리를 하지 않아, 관리가 용이
동시에 여러 품목을 주문(공급업체가 한 곳일 때)
> (s, S) 시스템 (조건부 보충시스템)
( Q재발주점 s, P목표재고수준 S) - 재발주점에 도달했을 때 목표재고수준의 차이만큼 주문
고정된 시간 간격마다 재고수준 조사 -> 재고수준이 사전에 정의한 재발주점(s) 이하
-> 재고를 목표재고수준(S)까지 끌어올릴 수 있을만큼 주문
참고 도서 : 생산운영관리, 유성열외, 이프레스, 2015
'전공 ✏️ > 생산 운영관리' 카테고리의 다른 글
공급사슬관리 (0) | 2022.06.20 |
---|---|
자재소요계획 (0) | 2022.06.20 |
총괄생산계획(APP)과 기준생산계획(MPS) (0) | 2022.06.19 |
입지선정 및 설비배치 (0) | 2022.05.01 |
생산능력 (0) | 2022.04.30 |